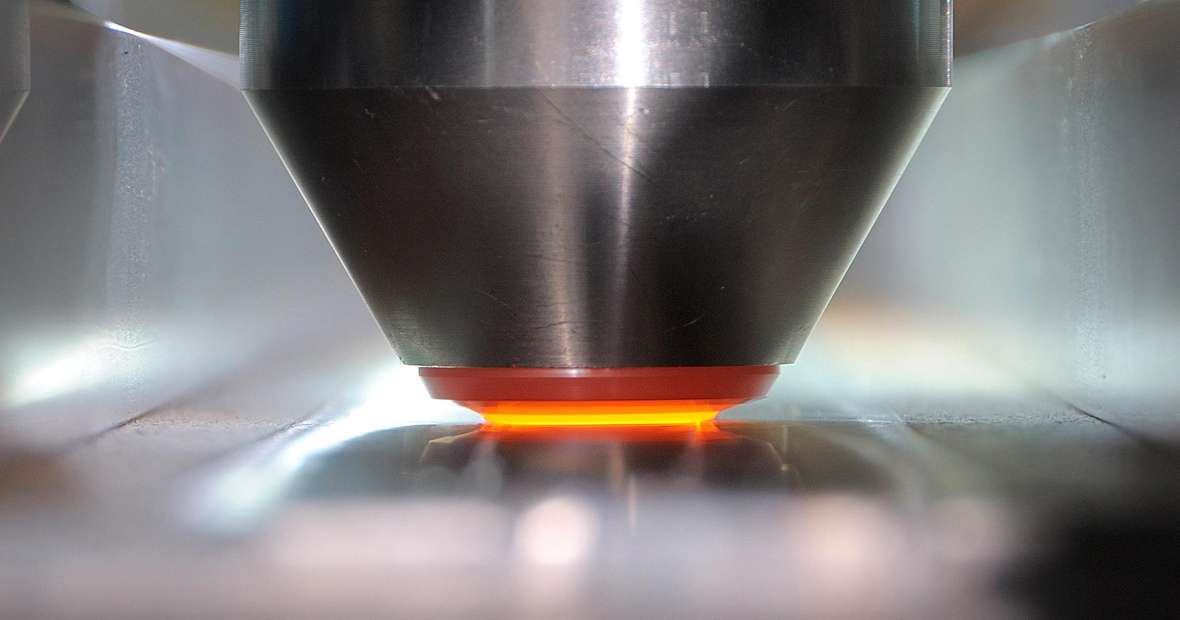
Bearing witness to a revolutionary shift in aerospace assembly techniques, Friction Stir Welding (FSW) continues to redefine boundaries. This groundbreaking process, with its unique ability to optimize weld strength and quality, has become a cornerstone in modern aircraft manufacturing. Its innovative applications are evident in the latest aerospace designs, demonstrating a seismic shift from traditional methods. Despite the promising prospects, FSW is not without its challenges. Material compatibility issues, thermal management during the process, and enhancing tool durability for high-strength aerospace alloys, remain persistent hurdles. Yet, the continuous advancements in tool and machine technology provide a beacon of hope for overcoming these obstacles. Throughout the progress, one thing remains clear - FSW and traditional welding methods are on a trajectory of divergence, each with their own unique merits and challenges within the aerospace sector.
Exploring friction stir welding: revolutionizing aerospace assembly
A technological leap in the aerospace industry, Friction stir welding (FSW) is revolutionizing assembly processes. A shift from traditional welding methods, FSW offers significant benefits in aircraft manufacturing, optimizing weld strength and quality. The process, which relies on friction and agitation, has transformed the way critical components for spacecraft and airplanes are manufactured.
Key benefits of FSW in aircraft manufacturing
A major advantage of FSW over conventional welding techniques is its impact on the durability and strength of joints in aerospace structures. This innovation significantly enhances the longevity of the assembly, marking a notable advancement in the field.
Optimizing weld strength and quality with FSW techniques
FSW is highly regarded for its ability to improve the quality of the weld, particularly in critical parts of the aircraft. It has set a new standard in the industry, aiding in the creation of more robust and efficient designs.
Innovative applications of FSW in modern aerospace designs
While the implementation of FSW in aerospace assembly poses certain technical challenges, the industry has been quick to devise innovative solutions. Looking ahead, emerging research and technologies are set to further enhance the benefits of FSW. The future of aerospace assembly will undoubtedly continue to be shaped by this groundbreaking technique.
Challenges in friction stir welding of aerospace materials
Friction stir welding (FSW) presents an innovative solution for the aerospace industry, promising high-strength weld joints on diverse materials. However, mastering the technique comes with its unique set of challenges. One of the first obstacles encountered relates to the complexity of welding dissimilar aerospace alloys. The industry often grapples with material compatibility issues, as aluminum alloys don't readily bind with metals of different compositions. The quest for quality control in the welded joints of aerospace composite materials further complicates the process. Ensuring the integrity of these joints under the harsh conditions of space travel is paramount for safety and functionality.
Overcoming material compatibility issues in FSW
Addressing these compatibility issues requires the optimization of welding parameters specifically for high-strength aluminum alloys. The process becomes a delicate balance of managing residual stresses and deformations in the welded structures. The technical limitations of friction stir welding equipment for large aerospace structures only add to the challenge.
Addressing thermal management during the welding process
Another significant hurdle lies in thermal management during the welding process. Excessive heat can degrade the material, compromising the integrity of the weld joint. Hence, maintaining optimal temperature conditions throughout the process is vital for a successful outcome.
Enhancing tool durability for high-strength aerospace alloys
Lastly, the durability of the welding tool becomes a concern when working with high-strength aerospace alloys. Specialized skills development for the operation of friction stir welding in the aerospace industry is crucial to navigate these challenges and ensure the long-term reliability of the welded structures.
Advancements in tool and machine technology for enhanced fsw processes
Within the realm of aerospace, friction stir welding (FSW) represents a significant advancement. The development of novel alloys for FSW tools, which enhance wear resistance and longevity in high-temperature environments, marks a major leap forward in the industry.
FSW tool design innovation, especially those incorporating optimized shoulder and pin geometries, contribute to superior material flow and weld quality. Advancements in FSW machine control systems, allowing for real-time adjustments of welding parameters, such as rotation speed and downward force, significantly increase efficiency. This is particularly evident in the heat-affected zone, where mechanical and thermal evolution can be accurately predicted using advanced modeling and simulation technology.
Real-time monitoring systems integration into FSW processes aids in defect detection during the welding process, thereby reducing the need for post-welding quality checks. High-tech cooling techniques are being adopted to regulate temperature within the welding zone, minimizing deformations and enhancing the mechanical properties of the joint. All these advancements in FSW tool and machine technology are enhancing processes, thus elevating the field of friction stir welding to new heights.
Comparative analysis of fsw and traditional welding methods in aerospace
In the realm of welding technology, an innovative trend has been observed in recent years - the emergence of Friction Stir Welding (FSW). This process, which is a solid-state joining technique, is being used with increasing frequency within the aerospace sector.
An examination of weld joint quality demonstrates that FSW-produced joints offer superior tensile strength properties compared to those welded using traditional methods. A sterling advantage of FSW lies in its adaptability to different materials; alloys that present challenges to conventional welding techniques are efficiently joined using FSW.
Structural integrity is a critical factor in aerospace construction. In a study comparing the incidence of weld defects, such as cracks and porosities, FSW exhibited fewer imperfections than its traditional counterparts. Operational costs and production time, too, favor FSW; this advanced method of welding proves more cost-effective and time-efficient for aerospace applications.
When discussing the application to large structures, FSW stands superior. This technique can manage large weld surfaces, overcoming the limitations of traditional methods in aircraft construction. Additionally, FSW exhibits an environmental advantage. The ecological footprint of FSW, in terms of air emissions and energy consumption, is significantly lower than conventional welding processes.